RESULTS AND DISCUSSION
⌅
Innovation is commonly understood as renewal, transformation.
The innovation process is preceded by research,
development, testing, and engineering. The development
of microwave electro-technological units with
hybrid working chambers (MWETU with HC) has gone
through these stages (Fig. 1). This construction allows for
simultaneous non-thermal Ultra High Frequency (UHF)
modification of the polymer material and thermal UHF
modification of the dielectric material in one installation.
An UHF electrotechnological device with a hybrid type
working chamber is cheaper, occupies a smaller area compared
to two separate devices that produce a total of the
same products with the same performance. The device has
a maximum efficiency, maximum energy and decent economic
efficacy, which determines its use.
In marketing research, attention should be paid primarily
to equipment that provides heat treatment of dielectrics
(heating, drying) and produces polymer materials and
products that are competitors of the MWETU with HC. At
this stage, the final decision is made which polymer and
dielectric objects will be processed in the planned to the
designed MWETU with HC.
The main part of the innovation activity is the equipment
(machine/unit) design. The work is completed by
signing an agreement on the introduction and serial production
of the MWETU with HC.
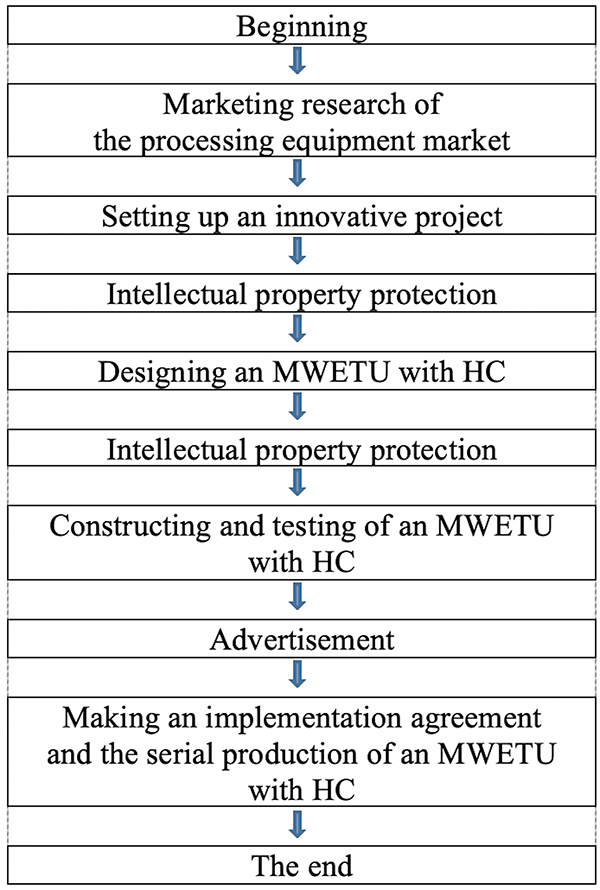
Figure 1. Stages of innovation activity in developing a microwave electrotechnological unit (MWETU) with hybrid working chambers (HC).
Constructing an MWETU with HC by upgrading an electro-thermal unit in a microwave is an option for developing this new class of MWETU. The added non-thermal MW modification processing module for treating polymer
increases the cost-efficiency of the modernized unit since it
provides higher profit without increasing energy consumption.
An entrepreneur supplies the commodity market with
at least two types of products. Let us consider constructing
an MWETU with HC on the example of upgraded microwave
electro-thermal equipment for timber drying.
Wood, as a cost-effective natural resource, is widely
used as a building and structural material in many industrial
and civil construction areas. The properties of dried
timber depend on the quality of microwave drying, being
the main operations for wood processing (Aniszewska &
Słowiński, 2016; He et al., 2017).
Thus, microwave drying can be implemented in an
MWETU with a discrete arrangement of several magnetrons
and a timber rotating mechanism in a radial chamber
(Tuhvatullin, 2020; 2021). This arrangement ensures
more uniform timber heating and reduces the drying time
by 38.8%, increases the output by 27.3% and enhances the
drying efficiency (Aipov et al., 2019; Tuhvatullin et al.,
2019).
It should be noted that drying is the longest and most expensive process in woodworking production.
Developed according to the microwave wood drying studies findings, a microwave timber dryer has a radial working chamber of 2.42 × 0.6 × 0.6 m with discretely located magnetrons, each of 1.2 kW/2450 MHz (Figs. 2 and 3) (Aipov et al., 2019).
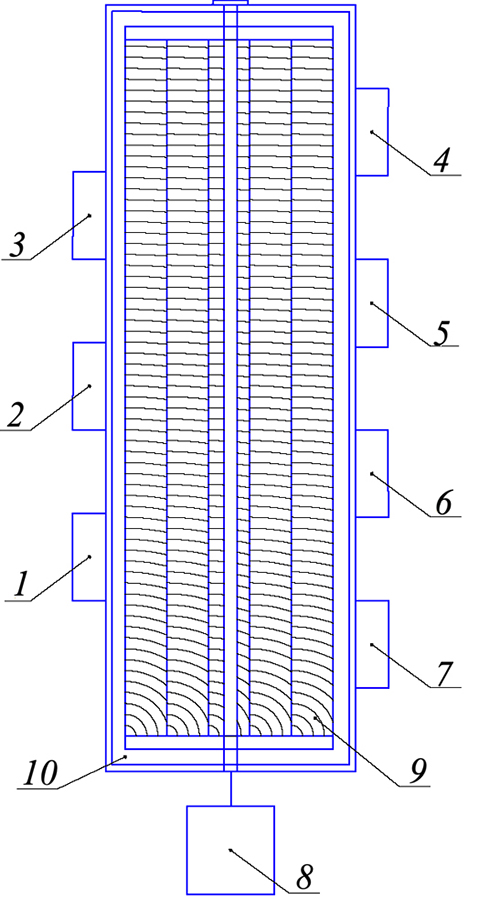
Figure 2. Functional chart of a microwave timber dryer: 1-7, sources of microwave energy on magnetrons; 8, electric drive; 9, a timber pile; 10, a radial working chamber.
In working chamber 1 of the microwave timber dryer, there is a mounted shaft 3 with fasteners for timber piles 4. Timber piles are rotated by an electric motor with a reducer 5. The working chamber has a cover for tight-sealing of the dryer.
The microwave dryer was made without horn emitters
to reduce the metal consumption, weight, and occupied
area. It decreased energy efficiency and lowered the cost
of the equipment. As a result, the dryer’s cost-efficiency
increased. The microwave dryer treated pine boards of 2
× 0.15 × 0.05 m each from the initial humidity of 84.5%
to 9%, the initial temperature of 22.5 ºC to 78 ºC for 14
hours, the boards did not get any defects.
If the microwave dryer, the heat MWETU, was equipped with a non-thermal MW modification processing module, the upgraded equipment becomes an MWETU with a hybrid chamber (HC).
Figure 4 shows a general view of the microwave timber
dryer. Figure 5 presents photos of the main construction
parts of the microwave dryer. Figure 6 shows a functional
chart of an MWETU with HC that produces a non-thermal
MW modification of polymer filaments and a thermal MW
modification (microwave drying of timber with a rotating
pile).
The microwave dryer used seven microwave energy
sources; therefore, the MWETU with HC based on this microwave
dryer has seven working chambers of a non-thermal
MW modification. Each chamber was assembled on
a segment of a rectangular homogeneous waveguide with flanges at its ends and longitudinal slits in the middle of wide walls, through which thin polymer threads, fibres, and other materials were stretched.
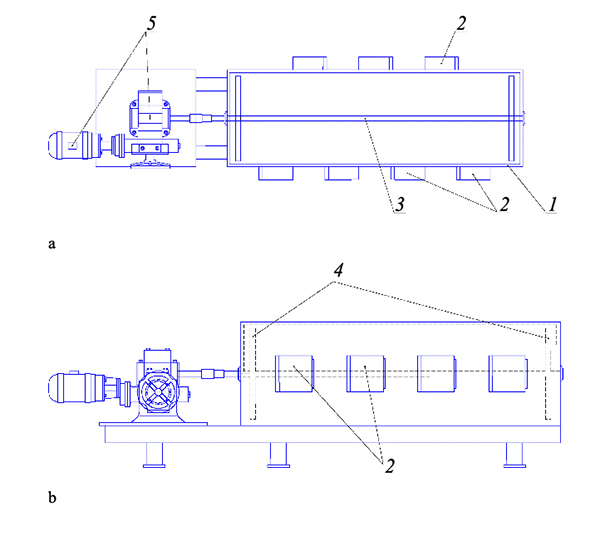
Figure 3. Microwave timber dryer: a, top view; b, side view (1, a camera; 2, a source of microwave energy; 3, a shaft; 4, fasteners for a timber pile; 5, an electric motor and a reducer).
While non-thermal MW modification in the waveguide
of 45 × 90 mm cross-section at 2450 MHz required less
microwave power than was produced by the microwave
generator of one microwave energy source (according to
Arkhangelskiy et al. (2012), non-thermal MW modification
of polycaproamide threads required 100 W at 0.9
cm/s of thread transportation rate), the MWETU with HC
would employ P=1, 2 kW for this MW modification or the non-thermal MW modification chamber would be built on
a directional coupler. Its main channel supplied 1.1 kW of
microwave power to the dryer and 100 W branches in the
side waveguide with slots on the broad wall. Here polycaproamide
threads underwent non-thermal modification.
Moreover, the microwave energy from the side channel
was fed into an additional working chamber of thermal
MW modification to treat dielectric material at a microwave
power of 100 W (Yudina & Arkhangelskiy, 2019).
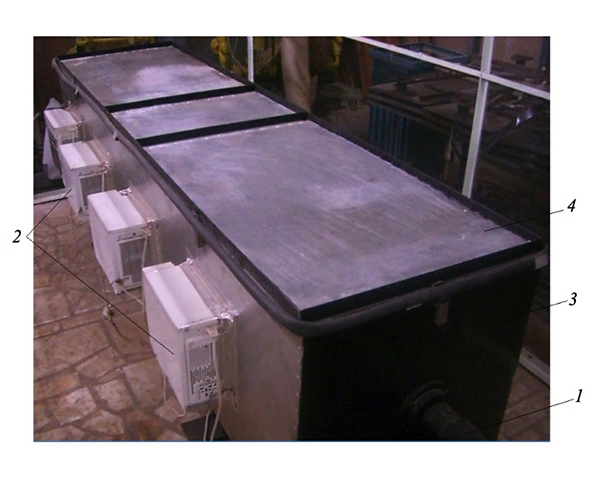
Figure 4. General view of the microwave dryer: 1, a shaft that provides rotation of a timber pile; 2, magnetrons; 3, the housing of the microwave dryer; 4, a cover of the working chamber made of steel mesh.
The length of the slots (the number of polymer threads) was determined by the results of marketing research, the demand for such modified threads on the commodity market.
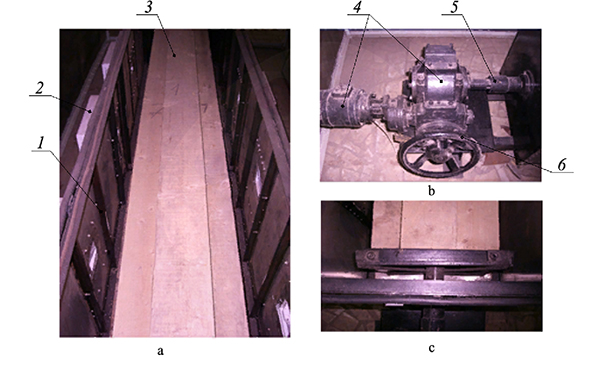
Figure 5. The main parts of the microwave dryer: a, internal view; b, electric drive; c, frame with fasteners (1, working chamber; 2, magnetron; 3, timber pile; 4, electric drive; 5, shaft; 6, mechanism for manual rotation of a timber pile).
It is important to note that each non-thermal MW modification
processing module can produce the same or different
polymer products. The MWETU with HC, in addition
to drying a timber pile, could produce from one to seven
different polymer objects. It requires equal microwave
power of emitters. Otherwise, the pile boards will heat up
and dry unevenly along the entire length, which will cause
board warping.
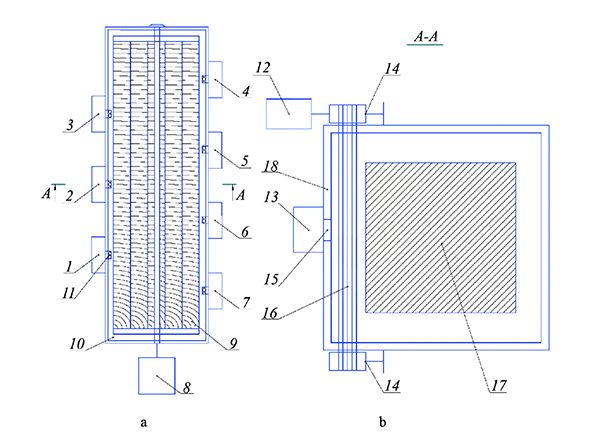
Figure 6. Functional chart of an upgraded microwave dryer MWETU with HC: a) MWETU with HC; b) crosssection according to A-A: 1-7, magnetrons (microwave energy sources); 8, electric drive; 9, dielectric (a timber pile); 10, a radial working chamber; 11, siting of modified threads or fibres; 12, electric drive of the transport system; 13, magnetron (microwave energy source); 14, transport system; 15, waveguide; 16, polymer threads; 17, a timber pile; 18, the wall of the MW unit's working chamber.
If polymer objects subjected to non-thermal MW modification
are located in the electromagnetic field of the microwave
timber dryer chamber, then the working chamber
turns into a combined hybrid chamber, and the microwave
dryer turns into an MWETU with HC, the functional chart
of which is shown in Fig. 7.
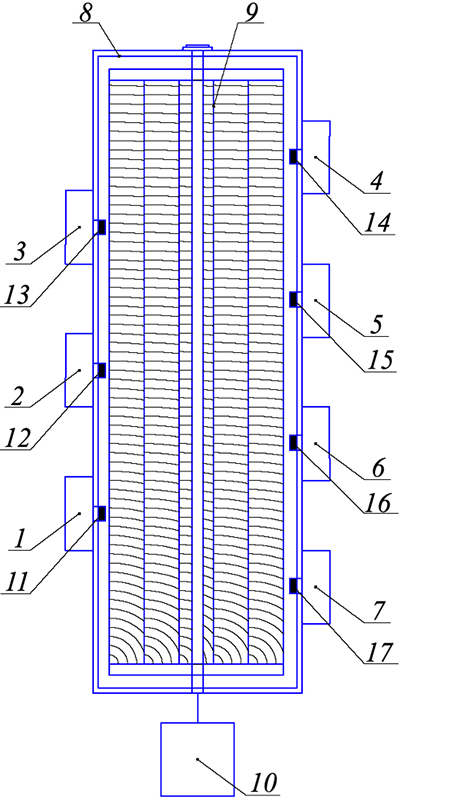
Figure 7. Functional chart of an MWETU with HC based on a microwave timber dryer: 1-7, sources of microwave energy on magnetrons; 8, working chamber; 9, timber pile; 10, electric drive; 11-17, siting of modified polymer objects.
If polymer threads are subjected to non-thermal MW
modification, they should be stretched in the microwave
electromagnetic field at a speed of 0.9 centimetres per second,
parallel to the voltage vector E. However, the rotation
of a timber pile continuously alters the boundary conditions
of the electrodynamics BVP (a vacuum switch), and
therefore the structure of the electromagnetic field is constantly
changing. This contributes to the drying of timber.
To conduct non-thermal MW modification of polymer
threads in such a combined hybrid working chamber, it
was necessary to choose siting directly near the aperture
of the radiating systems of the microwave dryer (Fig. 8).
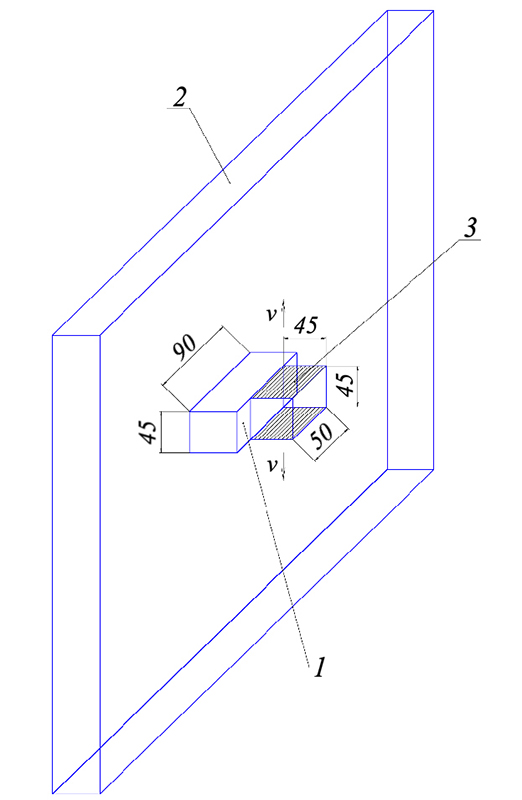
Figure 8. Siting of the polymer object in the microwave dryer chamber: 1, the emitter aperture (cross-section of a rectangular waveguide (45 × 90 mm); 2, the side wall of the working chamber; 3, siting of the polymer object; v, the motion speed of the modified object.
Suppose the water vapour evaporating from the timber
is dangerous for polymer objects undergoing non-thermal
MW modification in the neighbourhood. In that case,
polymer objects can be protected from water vapour by
a moisture-proof thin dielectric radio-transparent partition
separating the zones of the polymer objects from the zone where the timber pile undergoing thermal microwave modification rotates.
Let us compare the MWETU with HC shown in Figs. 6
and 7. The MWETU with HC in Fig. 7 favourably differed in
a smaller occupied area (the area of the microwave dryer was
reduced). It has less metal consumption, a more cross-sectional
area of the polymer object siting. Still, it has a more
complex transport system, being a significant drawback.
The absence of horn emitters in the microwave dryer,
matching its working chamber with the microwave generator,
creates an additional challenge for the MWETU with
HC, assembled according to the scheme shown in Fig. 6.
Indeed, the microwave energy reflected from the entrance
to the working chamber of the microwave dryer creates a
partially standing wave mode in the working chamber of
the non-thermal MW modification. It creates dependence
E(z) in this working chamber. When the length of the slots
in the chamber of the non-thermal MW modification is
greater than the wavelength in the waveguide, it will affect
the quality of polymer thread modification (Zhang et al.,
2018; Zlobina, 2018; Zhou et al., 2019).
The same situation occurs in the MWETU with HC (Fig. 7), if a quarter-wave matching transformer is not used in the working chamber of the microwave dryer (Fig. 9).
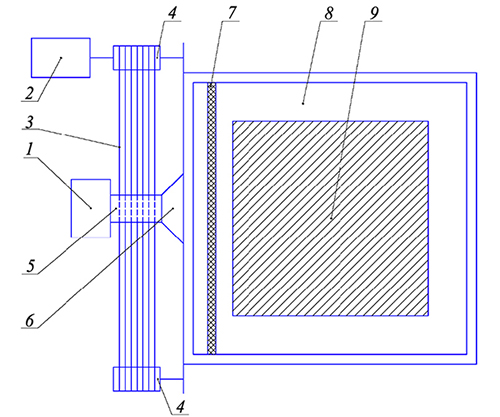
Figure 9. MWETU with HC based on a microwave timber dryer: 1, a microwave energy source; 2, electric drive; 3, polymer threads; 4, transport system for stretching polymer threads; 5, working chamber of non-thermal MW modification of polymer threads; 6, horn emitter; 7, quarter-wave matching transformer; 8, working chamber of the microwave dryer; 9, a timber pile.
Thus, the higher cost-efficiency of the unit due to used horn emitters and quarter-wave matching transformers ensures the quality of the products.
As for the calculations carried out during the design of
the MWETU with HC, the scientific foundations of the
MWETU for thermal microwave modification of dielectrics
are described, for example, in Arkhangelskiy (2011),
Zakharov (2017), Arkhangelskiy et al. (2018), Tuhvatullin
et al. (2019) and Tuhvatullin (2021). The procedure for calculating
the working chambers of non-thermal MW modification
is described in Arkhangelskiy et al. (2012). Technical
and economic calculations in microwave electro-technology
were considered in Arkhangelskiy & Kolesnikov (2017).
CONCLUSIONS
⌅
This paper discusses innovations in developing microwave electro-technological units with hybrid chambers. An alternative to the MWETU with HC is two microwave electro-technological units, one implementing a non-thermal MW modification of a polymer object and a thermal MW modification of a dielectric object.
The MWETU with HC is favourably different from
two separate pieces of equipment, since it needs only one
source of microwave energy. It occupies a smaller area,
has less metal consumption, is cheaper, and has the maximum
achievable energy efficiency. The MWETU with HC
provides two or more products to the commodity market,
bringing a very decent profit.
The main parameters of the MWETU with HC are as follows:
- a 2.42 × 0.6 × 0.6 m hybrid working chamber based
on a beam chamber with discretely located 1.2 kW magnetrons
at 2450 MHz on the side walls;
- an electric motor with a gearbox and a shaft with fasteners, providing rotation of a 2 × 0.15 × 0.05 m lumber stack for thermal microwave modification;
- a 45 × 90 mm waveguide at 2450 MHZ, the slits on its wide walls are used to transport 0.9 cm/s of polycaproamide strings for non-thermal microwave modification.
The goal of innovation activity can be achieved in two ways. Firstly, guided by the results of marketing research of the commodity market, polymer and dielectric objects are selected, which must undergo non-thermal and thermal microwave modifications in the projected microwave ETU (electrical installation) with KGT (readiness factor), after which the design, manufacture, testing, and implementation of the installation is carried out.
This research discusses the second way of achieving
the goal of innovation activity, being of great practical interest:
modernization of the existing microwave and thermal
microwave modification, associated with equipping
this installation with a non-thermal microwave modification
technological unit. Possible opportunities are shown
by the example of a redeveloped microwave timber dryer,
in which a timber pile is manually or automatically rotated
in the working chamber.
These two directions in creating an MWETU with HC
are not competitors to each other. The example of a modernized
microwave timber dryer given in this paper shows
the expediency of upgrading existing MWETU to turn
them into MWETU with HC and getting more profit, increasing
the cost-efficiency of the existing processing unit.
The results of marketing research of the commodity
market of polymer and dielectric materials, products can
show the demand for such products, which can be obtained
with a decent profit with the help of microwave
electro-technological equipment. The given study showed
how to arrange innovative activities to create an MWETU
with HC, a new class of microwave units that differ favorably
from MWETU, implementing only non-thermal microwave
modification of polymers or thermal microwave
modification dielectrics.
The present paper demonstrated the expediency of
achieving this goal by using the existing MWETU of thermal
MW modification, having modernized it. This innovative
activity direction was demonstrated by the modification
of a microwave dryer of lumber. The paper described
the options for such modernization: technological blocks
were placed between the microwave energy source and
the conventional microwave dryer chamber, for example,
for non-thermal microwave modification of polymer filaments,
or these filaments are placed inside the working
chamber of the microwave dryer, which makes the microwave
dryer turn into a microwave oven with a combined hybrid-type working chamber. The upgraded microwave dryer, the MWETU with HC, can produce up to seven different polymer threads and dry a timber pile.
This option of creating an MWETU with HC is not only of practical interest but also scientific since the scientific basis for designing an MWETU with HC is one of the present-day challenges in microwave electro-technology.
The practical modernization of the microwave dryer for a timber pile to build a microwave electro-technological unit with a hybrid chamber, on its basis carried out by the developer of the microwave dryer, will increase the variety of products and expand the possibilities of microwave electro-technology.